Iso 9001 Management Review Meeting Presentation Template
The ISO 9000 family of quality management systems (QMS) standards is designed to help organizations ensure that they meet the needs of customers and other stakeholders while meeting statutory and regulatory requirements related to a product or service.[1]ISO 9000 deals with the fundamentals of quality management systems,[2] including the seven quality management principles upon which the family of standards is based.[2][3][4] ISO 9001 deals with the requirements that organizations wishing to meet the standard must fulfill.[5]
If you want a copy of a management review template for recording your meeting results, please send a request to larry@whittingtonassociates.com. The template is a Word file. It includes clickable date fields for Review Date and Next Review, as well as, entries for the Chairperson and Recorder.
Third-party certification bodies provide independent confirmation that organisations meet the requirements of ISO 9001. Over one million organisations worldwide[6] are independently certified, making ISO 9001 one of the most widely used management tools in the world today. However, the ISO certification process has been criticised[7][8] as being wasteful and not being useful for all organizations.[9][10]
- 7Evolution of ISO 9000 standards
- 10Effectiveness
Background[edit]
ISO 9000 was first published in 1987 by ISO (International Organisation for Standardization).[11] It was based on the BS 5750 series of standards from BSI that were proposed to ISO in 1979.[12] However, its history can be traced back some twenty years before that, to the publication of government procurement standards, such as the United States Department of Defense MIL-Q-9858 standard in 1959, and the UK's Def Stan 05-21 and 05-24. Large organizations which supplied government procurement agencies often had to comply with a variety of quality assurance requirements for each contract awarded which led the defence industry to adopt mutual recognition of NATO AQAP, MIL-Q and Def Stan standards. Eventually, ISO 9000 was adopted as a suitable option, instead of forcing contractors to adopt multiple - and often similar - requirements.[13]
Reasons for use[edit]
The global adoption of ISO 9001 may be attributable to a number of factors. In the early days, the ISO 9001 (9002 and 9003) requirements were intended to be used by procuring organizations[clarification needed], as the basis of contractual arrangements with their suppliers. This helped reduce the need for 'supplier development'[vague] by establishing basic requirements for a supplier to assure product quality. The ISO 9001 requirements could be tailored to meet specific contractual situations, depending on the complexity of product, business type (design responsibility, manufacture only, distribution, servicing etc.) and risk to the procurer. If a chosen supplier was weak on the controls of their measurement equipment (calibration), and hence QC/inspection results, that specific requirement would be invoked in the contract. The adoption of a single Quality Assurance requirement also lead to cost savings throughout the supply chain by reducing the administrative burden of maintaining multiple sets of quality manuals and procedures.
A few years later, the UK Government took steps to improve national competitiveness following publication of cmd 8621, and Third Party Certification of Quality Management Systems was born, under the auspices of the National Accreditation Council of Certification Bodies (NACCB) which has become the United Kingdom Accreditation Service (UKAS) .
In addition to many stakeholders' benefits, a number of studies have identified significant financial benefits for organizations certified to ISO 9001, with a 2011 survey from the British Assessment Bureau showing 44% of their certified clients had won new business.[14] Corbett et al. showed that certified organizations achieved superior return on assets[15] compared to otherwise similar organizations without certification.[16] Heras et al. found similarly superior performance[16] and demonstrated that this was statistically significant and not a function of organization size.[17] Naveha and Marcus claimed that implementing ISO 9001 led to superior operational performance in the U.S. automotive industry.[18] Sharma identified similar improvements in operating performance and linked this to superior financial performance.[19] Chow-Chua et al. showed better overall financial performance was achieved for companies in Denmark.[20] Rajan and Tamimi (2003) showed that ISO 9001 certification resulted in superior stock market performance and suggested that shareholders were richly rewarded for the investment in an ISO 9001 system.[21]
While the connection between superior financial performance and ISO 9001 may be seen from the examples cited, there remains no proof of direct causation, though longitudinal studies, such as those of Corbett et al. (2005)[16] may suggest it. Other writers, such as Heras et al. (2002),[17] have suggested that while there is some evidence of this, the improvement is partly driven by the fact that there is a tendency for better performing companies to seek ISO 9001 certification.
The mechanism for improving results has also been the subject of much research. Lo et al. (2007) identified operational improvements (e.g., cycle time reduction, inventory reductions) as following from certification.[22] Internal process improvements in organizations lead to externally observable improvements.[23][24] The benefit of increased international trade and domestic market share, in addition to the internal benefits such as customer satisfaction, interdepartmental communications, work processes, and customer/supplier partnerships derived, far exceeds any and all initial investment.[25]
Global adoption[edit]

The increase in ISO 9001 certification is shown in the tables below.
2000[26] | 2001[26] | 2002[26] | 2003[26] | 2004[27] | 2005[27] | 2006[27] | 2007[27] |
---|---|---|---|---|---|---|---|
409,421 | 510,616 | 561,747 | 567,985 | 660,132 | 773,867 | 896,929 | 951,486 |
2008[28] | 2009[28] | 2010[29] | 2011[29] | 2012[30] | 2013[31] | 2014[31] | |
982,832 | 1,064,785 | 1,118,510 | 1,111,698 | 1,096,987 | 1,126,460 | 1,138,155 |
Rank | Country | No. of certificates |
---|---|---|
1 | China | 342,800 |
2 | Italy | 168,960 |
3 | Germany | 55,363 |
4 | Japan | 45,785 |
5 | India | 41,016 |
6 | United Kingdom | 40,200 |
7 | Spain | 36,005 |
8 | United States | 33,008 |
9 | France | 29,122 |
10 | Australia | 19,731 |
Rank | Country | No. of certificates |
---|---|---|
1 | China | 297,037 |
2 | Italy | 138,892 |
3 | Russian Federation | 62,265 |
4 | Spain | 59,854 |
5 | Japan | 59,287 |
6 | Germany | 50,583 |
7 | United Kingdom | 44,849 |
8 | India | 33,250 |
9 | United States | 25,101 |
10 | Korea, Republic of | 24,778 |
Rank | Country | No. of certificates |
---|---|---|
1 | China | 257,076 |
2 | Italy | 130,066 |
3 | Japan | 68,484 |
4 | Spain | 59,576 |
5 | Russian Federation | 53,152 |
6 | Germany | 47,156 |
7 | United Kingdom | 41,193 |
8 | India | 37,493 |
9 | United States | 28,935 |
10 | Korea, Republic of | 23,400 |
ISO 9000 series Quality Management Principles[edit]
The ISO 9000 series are based on seven quality management principles (QMP)[33]
The seven quality management principles are:
- QMP 1 – Customer focus
- QMP 2 – Leadership
- QMP 3 – Engagement of people
- QMP 4 – Process approach
- QMP 5 – Improvement
- QMP 6 – Evidence-based decision making
- QMP 7 – Relationship management
Principle 1 – Customer focus
- Organizations depend on their customers and therefore should understand current and future customer needs, should meet customer requirements and strive to exceed customer expectations.
Principle 2 – Leadership
- Leaders establish unity of purpose and direction of the organization. They should create and maintain the internal environment in which people can become fully involved in achieving the organization's objectives.
Principle 3 – Engagement of people
- People at all levels are the essence of an organization and their full involvement enables their abilities to be used for the organization's benefit.
Principle 4 – Process approach
- A desired result is achieved more efficiently when activities and related resources are managed as a process.
Principle 5 – Improvement
- Improvement of the organization's overall performance should be a permanent objective of the organization.
Principle 6 – Evidence-based decision making
- Effective decisions are based on the analysis of data and information.
Principle 7 – Relationship management
- An organization and its external providers (suppliers, contractors, service providers) are interdependent and a mutually beneficial relationship enhances the ability of both to create value.
Contents of ISO 9001:2015[edit]
ISO 9001:2015 Quality management systems — Requirements is a document of approximately 30 pages which is available from the national standards organization in each country. Only ISO 9001 is directly audited against for third party assessment purposes.
Contents of ISO 9001:2015 are as follows:
- Section 1: Scope
- Section 2: Normative references
- Section 3: Terms and definitions
- Section 4: Context of the organization
- Section 5: Leadership
- Section 6: Planning
- Section 7: Support
- Section 8: Operation
- Section 9: Performance evaluation
- Section 10: Continual Improvement
Essentially, the layout of the standard is similar to the previous ISO 9001:2008 standard in that it follows the Plan, Do, Check, Act cycle in a process-based approach but is now further encouraging this to have risk-based thinking (section 0.3.3 of the introduction). The purpose of the quality objectives is to determine the conformity of the requirements (customers and organizations), facilitate effective deployment and improve the quality management system.[34][35]
Before the certification body can issue or renew a certificate, the auditor must be satisfied that the company being assessed has implemented the requirements of sections 4 to 10. Sections 1 to 3 are not directly audited against, but because they provide context and definitions for the rest of the standard, not that of the organization, their contents must be taken into account.
The standard no longer specifies that the organization shall issue and maintain documented procedures, however, ISO 9001:2015 requires the organization to document any other procedures required for its effective operation. The standard also requires the organization to issue and communicate a documented quality policy, a quality management system scope, and quality objectives. The standard no longer requires compliant organizations to issue a formal Quality Manual. The standard does require retention of numerous records, as specified throughout the standard. New for the 2015 release is a requirement for an organization to assess risks and opportunities (section 6.1) and to determine internal and external issues relevant to its purpose and strategic direction (section 4.1). The organization must demonstrate how the standard's requirements are being met, while the external auditor's role is to determine the quality management system's effectiveness. More detailed interpretation and implementation examples are often sought by organizations seeking more information in what can be a very technical area.
Certification[edit]
The International Organization for Standardization (ISO) does not certify organisations itself. Numerous certification bodies exist, which audit organisations and, upon success, issue ISO 9001 compliance certificates. Although commonly referred to as 'ISO 9000' certification, the actual standard to which an organization's quality management system can be certified is ISO 9001:2015 (ISO 9001:2008 expired around September 2018). Many countries have formed accreditation bodies to authorize ('accredit') the certification bodies. Both the accreditation bodies and the certification bodies charge fees for their services. The various accreditation bodies have mutual agreements with each other to ensure that certificates issued by one of the accredited certification bodies (CB) are accepted worldwide. Certification bodies themselves operate under another quality standard, ISO/IEC 17021,[36] while accreditation bodies operate under ISO/IEC 17011.[37]
An organization applying for ISO 9001 certification is audited based on an extensive sample of its sites, functions, products, services and processes. The auditor presents a list of problems (defined as 'nonconformities', 'observations', or 'opportunities for improvement') to management. If there are no major nonconformities, the certification body will issue a certificate. Where major nonconformities are identified, the organization will present an improvement plan to the certification body (e.g., corrective action reports showing how the problems will be resolved); once the certification body is satisfied that the organization has carried out sufficient corrective action, it will issue a certificate. The certificate is limited by a certain scope (e.g., production of golf balls) and will display the addresses to which the certificate refers.
An ISO 9001 certificate is not a once-and-for-all award but must be renewed at regular intervals recommended by the certification body, usually once every three years. There are no grades of competence within ISO 9001: either a company is certified (meaning that it is committed to the method and model of quality management described in the standard) or it is not. In this respect, ISO 9001 certification contrasts with measurement-based quality systems.
Evolution of ISO 9000 standards[edit]
The ISO 9000 standard is continually being revised by standing technical committees and advisory groups, who receive feedback from those professionals who are implementing the standard.
1987 version[edit]
ISO 9000:1987 had the same structure as the UK Standard BS 5750, with three 'models' for quality management systems, the selection of which was based on the scope of activities of the organization:
- ISO 9001:1987 Model for quality assurance in design, development, production, installation, and servicing was for companies and organizations whose activities included the creation of new products.
- ISO 9002:1987 Model for quality assurance in production, installation, and servicing had basically the same material as ISO 9001 but without covering the creation of new products.
- ISO 9003:1987 Model for quality assurance in final inspection and test covered only the final inspection of finished product, with no concern for how the product was produced.
ISO 9000:1987 was also influenced by existing U.S. and other Defense Standards ('MIL SPECS'), and so was well-suited to manufacturing. The emphasis tended to be placed on conformance with procedures rather than the overall process of management, which was likely the actual intent.[citation needed]
1994 version[edit]
ISO 9000:1994 emphasized quality assurance via preventive actions, instead of just checking final product, and continued to require evidence of compliance with documented procedures. As with the first edition, the down-side was that companies tended to implement its requirements by creating shelf-loads of procedure manuals, and becoming burdened with an ISO bureaucracy. In some companies, adapting and improving processes could actually be impeded by the quality system.[citation needed]
2000 version[edit]
ISO 9001:2000 replaced all three former standards of 1994 issue, ISO 9001, ISO 9002 and ISO 9003. Design and development procedures were required only if a company does, in fact, engage in the creation of new products. The 2000 version sought to make a radical change in thinking by actually placing front and centre the concept of process management (the monitoring and optimisation of a company's tasks and activities, instead of just inspection of the final product). The 2000 version also demanded involvement by upper executives in order to integrate quality into the business system and avoid delegation of quality functions to junior administrators. Another goal was to improve effectiveness via process performance metrics: numerical measurement of the effectiveness of tasks and activities. Expectations of continual process improvement and tracking customer satisfaction were made explicit.
ISO 9000 Requirements include:
- Approve documents before distribution;
- Provide correct version of documents at points of use;
- Use your records to prove that requirements have been met; and
- Develop a procedure to control your records.
2008 version[edit]
ISO 9001:2008 in essence re-narrates ISO 9001:2000. The 2008 version only introduced clarifications to the existing requirements of ISO 9001:2000 and some changes intended to improve consistency with ISO 14001:2004. There were no new requirements. For example, in ISO 9001:2008, a quality management system being upgraded just needs to be checked to see if it is following the clarifications introduced in the amended version.
ISO 9001 is supplemented directly by two other standards of the family:
- ISO 9000:2005 'Quality management systems. Fundamentals and vocabulary'
- ISO 9004:2009 'Managing for the sustained success of an organization. A quality management approach'
Other standards, like ISO 19011 and the ISO 10000 series, may also be used for specific parts of the quality system.
2015 version[edit]
In 2012, ISO TC 176 - responsible for ISO 9001 development - celebrated 25 years of implementing ISO 9001,[38] and concluded that it was necessary to create a new QMS model for the next 25 years. They subsequently commenced the official work on creating a revision of ISO 9001, starting with the new QM principles. This moment was considered by important specialists in the field as 'beginning of a new era in the development of quality management systems.'[39] As a result of the intensive work from this technical committee, the revised standard ISO 9001:2015 was published by ISO on 23 September 2015. The scope of the standard has not changed; however, the structure and core terms were modified to allow the standard to integrate more easily with other international management systems standards.[40]
The new ISO 9001:2015 management system standard helps ensure that consumers get reliable, desired quality goods and services. This further increases benefits for a business.[41]
The 2015 version is also less prescriptive than its predecessors and focuses on performance. This was achieved by combining the process approach with risk-based thinking, and employing the Plan-Do-Check-Act cycle at all levels in the organization.[42]
Some of the key changes include:
- High-Level Structure of 10 clauses is implemented. Now all new standards released by ISO will have this high-level structure
- Greater emphasis on building a management system suited to each organization's particular needs
- A requirement that those at the top of an organization be involved and accountable, aligning quality with wider business strategy
- Risk-based thinking throughout the standard makes the whole management system a preventive tool and encourages continuous improvement
- Less prescriptive requirements for documentation: the organisation can now decide what documented information it needs and what format it should be in
- Alignment with other key management system standards through the use of a common structure and core text[43]
- Inclusion of Knowledge Management principles
- Quality Manual & Management representative (MR) are no longer mandatory
Auditing[edit]
Two types of auditing are required to become registered to the standard: auditing by an external certification body (external audit) and audits by internal staff trained for this process (internal audits). The aim is a continual process of review and assessment to verify that the system is working as it is supposed to, to find out where it can improve, and to correct or prevent identified problems. It is considered healthier for internal auditors to audit outside their usual management line, so as to bring a degree of independence to their judgements.
Industry-specific interpretations[edit]
The ISO 9001 standard is generic; its parts must be carefully interpreted to make sense within a particular organization. Developing software is not like making cheese or offering counseling services, yet the ISO 9001 guidelines, because they are business management guidelines, can be applied to each of these. Diverse organizations—police departments (United States), professional soccer teams (Mexico), and city councils (UK)—have successfully implemented ISO 9001:2000 systems.
Over time, various industry sectors have wanted to standardise their interpretations of the guidelines within their own marketplace. This is partly to ensure that their versions of ISO 9000 have their specific requirements, but also to try and ensure that more appropriately trained and experienced auditors are sent to assess them.
- The TickIT guidelines are an interpretation of ISO 9000 produced by the UK Board of Trade to suit the processes of the information technology industry, especially software development.
- AS9000 is the Aerospace Basic Quality System Standard, an interpretation developed by major aerospace manufacturers. Those major manufacturers include AlliedSignal, Allison Engine, Boeing, General Electric Aircraft Engines, Lockheed-Martin, McDonnell Douglas, Northrop Grumman, Pratt & Whitney, Rockwell-Collins, Sikorsky Aircraft, and Sundstrand. The current version is AS9100D.
- PS 9000 * QS 9000 is an interpretation agreed upon by major automotive manufacturers (GM, Ford, Chrysler). It includes techniques such as FMEA and APQP. QS 9000 is now replaced by ISO/TS 16949.
- ISO/TS 16949:2009 is an interpretation agreed upon by major automotive manufacturers (American and European manufacturers); the latest version is based on ISO 9001:2008. The emphasis on a process approach is stronger than in ISO 9001:2008. ISO/TS 16949:2009 contains the full text of ISO 9001:2008 and automotive industry-specific requirements. After the new edition of ISO 9001:2015 the ISO/TS 16949:2009 was also completely revised and reissued by IATF (International Automotive Task Force) IATF 16949:2016 is now a stand-alone standard which doesn't include the ISO 9001:2015 requirements but still refer to them and works as additional automotive specific requirement to ISO 9001.
- TL 9000 is the Telecom Quality Management and Measurement System Standard, an interpretation developed by the telecom consortium, QuEST Forum. In 1998 QuEST Forum developed the TL 9000 Quality Management System to meet the supply chain quality requirements of the worldwide telecommunications industry. The TL 9000 standard is made up of two handbooks: the QMS Requirements Handbook, and the QMS Measurement Handbook. The current versions of the Requirements and Measurements Handbooks are 5.0. Unlike ISO 9001 or other sector-specific standards, TL 9000 includes standardized product and process measurements that must be reported into a central repository, which allows organizations to benchmark their performance in key process areas against peer organizations. It is important to note that TL 9000 R5.0 contains the full text of ISO 9001:2008.
- ISO 13485:2016 is the medical industry's equivalent of ISO 9001. ISO 13485:2016 is a stand-alone standard. Because ISO 13485 is relevant to medical devices manufacturers (unlike ISO 9001, which is applicable to any industry), and because of the differences between the two standards relating to continual improvement, compliance with ISO 13485 does not necessarily mean compliance with ISO 9001 (and vice versa).
- ISO/IEC 90003:2014 provides guidelines for the application of ISO 9001 to computer software.
- ISO/TS 29001 is quality management system requirements for the design, development, production, installation, and service of products for the petroleum, petrochemical, and natural gas industries. It is equivalent to API Spec Q1 without the Monogram annex.
- ISO 22000 Food Safety Management Systems.
Effectiveness[edit]
The debate on the effectiveness of ISO 9000 commonly centres on the following questions:
- Are the quality principles in ISO 9001 of value?
- Does it help to implement an ISO 9001-compliant quality management system?
- Does it help to obtain ISO 9001 certification?
The effectiveness of the ISO system being implemented depends on a number of factors, the most significant of which are:
- Commitment of senior management to monitor, control, and improve quality. Organizations that implement an ISO system without this desire and commitment often take the cheapest road to get a certificate on the wall and ignore problem areas uncovered in the audits.
- How well the ISO system integrates into current business practices. Many organizations that implement ISO try to make their system fit into a cookie-cutter quality manual instead of creating a manual that documents existing practices and only adds new processes to meet the ISO standard when necessary.
- How well the ISO system focuses on improving the customer experience. The broadest definition of quality is 'Whatever the customer perceives good quality to be.' This means that a company doesn't necessarily have to make a product that never fails; some customers will have a higher tolerance for product failures if they always receive shipments on-time or have a positive experience in some other dimension of customer service. An ISO system should take into account all areas of the customer experience and the industry expectations, and seek to improve them on a continual basis. This means taking into account all processes that deal with the three stakeholders (customers, suppliers, and organization); only then will a company be able to sustain improvements in the customer's experience.
- How well the auditor finds and communicates areas of improvement. While ISO auditors may not provide consulting to the clients they audit, there is the potential for auditors to point out areas of improvement. Many auditors simply rely on submitting reports that indicate compliance or non-compliance with the appropriate section of the standard; however, to most executives, this is like speaking a foreign language. Auditors that can clearly identify and communicate areas for improvement in language and terms executive management understands facilitate action on improvement initiatives by the companies they audit. When management doesn't understand why they were non-compliant and the business implications associated with non-compliance, they simply ignore the reports and focus on what they do understand.
Advantages[edit]
Proper quality management can improve business, often having a positive effect on investment, market share, sales growth, sales margins, competitive advantage, and avoidance of litigation.[44] The quality principles in ISO 9000:2000 are also sound, according to Wade [45] and Barnes, who says that 'ISO 9000 guidelines provide a comprehensive model for quality management systems that can make any company competitive'.[46] Sroufe and Curkovic, (2008) found benefits ranging from registration required to remain part of a supply base, better documentation, to cost benefits, and improved involvement and communication with management.[44] According to ISO[47] the 2015 version of the standard brings the following benefits:
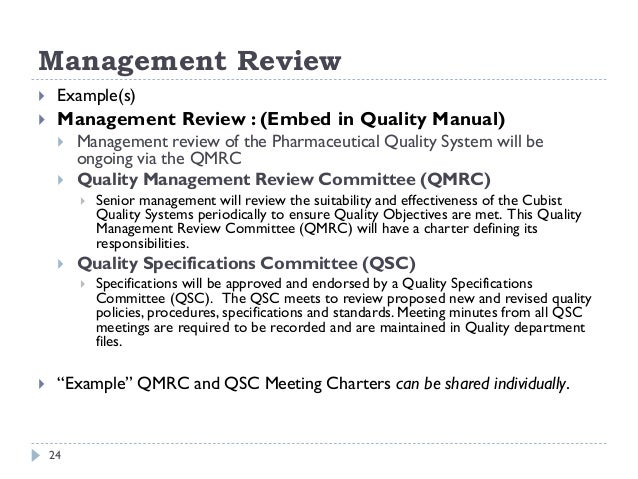
- By assessing their context, organizations can define who is affected by their work and what they expect. This enables clearly stated business objectives and the identification of new business opportunities.
- Organizations can identify and address the risks associated with their organization.
- By putting customers first, organizations can make sure they consistently meet customer needs and enhance customer satisfaction. This can lead to more repeat customers, new clients and increased business for the organization.
- Organizations work in a more efficient way as all their processes are aligned and understood by everyone. This increases productivity and efficiency, bringing internal costs down.
- Organizations will meet necessary statutory and regulatory requirements.
- Organizations can expand into new markets, as some sectors and clients require ISO 9001 before doing business.
Criticisms of ISO 9001 certification[edit]
A common criticism of ISO 9000 and 9001 is the amount of money, time, and paperwork required for a complete implementation, and later when needed; ISO 9001 certification.[7] Dalgleish cites the 'inordinate and often unnecessary paperwork burden' of ISO, and says that 'quality managers feel that ISO's overhead and paperwork are excessive and extremely inefficient'.[48] The level of minimum documentation for a minimum scope organization has been greatly reduced, going from ISO 9001:2000 to ISO 9001:2008 to ISO 9001:2015.[citation needed]
According to Barnes, 'Opponents claim that it is only for documentation. Proponents believe that if a company has documented its quality systems, then most of the paperwork has already been completed'.[46] Wilson suggests that ISO standards 'elevate inspection of the correct procedures over broader aspects of quality', and therefore, 'the workplace becomes oppressive and quality is not improved'.[8]
One study showing reasons for not adopting this standard include the risks and uncertainty of not knowing if there are direct relationships to improved quality, and what kind and how many resources will be needed. Additional risks include how much certification will cost, increased bureaucratic processes and risk of poor company image if the certification process fails.[44] According to John Seddon, ISO 9001 promotes specification, control, and procedures rather than understanding and improvement.[9] Wade argues that ISO 9000 is effective as a guideline, but that promoting it as a standard 'helps to mislead companies into thinking that certification means better quality, .. [undermining] the need for an organization to set its own quality standards'.[45] In short, Wade argues that reliance on the specifications of ISO 9001 does not guarantee a successful quality system.
The standard is seen as especially prone to failure when a company is interested in certification before quality.[9] Certifications are in fact often based on customer contractual requirements rather than a desire to actually improve quality.[46][49] 'If you just want the certificate on the wall, chances are you will create a paper system that doesn't have much to do with the way you actually run your business', said ISO's Roger Frost.[49] Certification by an independent auditor is often seen as the problem area, and according to Barnes, 'has become a vehicle to increase consulting services'.[46]
Dalgleish argues that while 'quality has a positive effect on return on investment, market share, sales growth, better sales margins and competitive advantage,' 'taking a quality approach is unrelated to ISO 9000 registration.'[50] In fact, ISO itself advises that ISO 9001 can be implemented without certification, simply for the quality benefits that can be achieved.[51]
Abrahamson argues that fashionable management discourse such as Quality Circles tends to follow a lifecycle in the form of a bell curve, possibly indicating a management fad.[52]
Pickrell argues[citation needed] that ISO systems merely gauge whether the processes are being followed. It does not gauge how good the processes are or whether the correct parameters are being measured and controlled to ensure quality. Furthermore, when unique technical solutions are involved in the creation of a new part, ISO does not validate the robustness of the technical solution which is a key part of advanced quality planning. It is not unheard of for an ISO-certified plant to display poor quality performance due to poor process selection and/or poor technical solutions.
See also[edit]
- Conformity assessment—Containing ISO published standards
- ISO 10006—Quality management—Guidelines to quality management in projects
- ISO 13485—Medical devices—Quality management systems—Requirements for regulatory purposes
- ISO 14001—Environmental management standards
- ISO 19011—Guidelines for quality management systems auditing and environmental management systems auditing
- ISO/TS 16949—Quality management system requirements for automotive-related products suppliers
- ISO/IEC 27001—Information security management
- ISO 39001—Road traffic safety management
- ISO 50001—Energy Audit
- AS 9100—aerospace industry implementation of ISO 9000/1
References[edit]
- ^Poksinska, Bozena; Dahlgaard, Jens Jörn; Antoni, Marc (2002). 'The state of ISO 9000 certification: A study of Swedish organisations'. The TQM Magazine. 14 (5): 297. doi:10.1108/09544780210439734.
- ^ abTsim, Y.C.; Yeung, V.W.S.; Leung, Edgar T.C. (2002). 'An adaptation to ISO 9001:2000 for certified organisations'. Managerial Auditing Journal. 17 (5): 245. doi:10.1108/02686900210429669.
- ^Quality Management Principles(PDF). International Organization for Standardization. 2015. ISBN978-92-67-10650-2.
- ^Beattie, Ken R. (1999). 'Implementing ISO 9000: A study of its benefits among Australian organizations'. Total Quality Management. 10: 95–106. doi:10.1080/0954412998090.
- ^'ISO 9000 - Quality management'. International Organization for Standardization.
- ^'ISO 9000 Quality Management'. ISO. International Organisation for Standardisation. Retrieved 22 May 2017.
- ^ abClifford, Stephanie (1 May 2005). 'So many standards to follow, so little payoff'. Inc.
- ^ abWilson, Ian (4 June 2010). 'Is ISO the way to go? Some say, Not So'. The Westgard Rules.[self-published source?]
- ^ abcSeddon, John (19 November 2000). 'The 'quality' you can't feel'. The Observer.
- ^'A Brief History of ISO 9000: Where did we go wrong?'. The Case Against ISO 9000 (2nd ed.). Oak Tree Press. 2000. ISBN978-1-86076-173-7.
- ^'BSOL Academic - BSI Group'. Bsieducation.org.
- ^'Standards, Training, Testing, Assessment and Certification - BSI Group'. Bsigroup.com.
- ^Stamatis, D H (8 August 1995). Understanding ISO 9000 and Implementing the Basics to Quality. CRC Press. ISBN9780824796563. Retrieved 14 February 2018.
- ^'ISO 9001 proven to help win new business'. British Assessment Bureau. 25 May 2011. Archived from the original on 28 July 2013.
- ^'BSI Case Study on the Benefits of ISO 9000 Registration - Interstate Worldwide Relocation'(PDF). BSi Management System. Archived from the original(PDF) on 19 May 2006.
- ^ abcCorbett, Charles J.; Montes-Sancho, María J.; Kirsch, David A. (2005). 'The Financial Impact of ISO 9000 Certification in the United States: An Empirical Analysis'(PDF). Management Science. 51 (7): 1607–16. doi:10.1287/mnsc.1040.0358. JSTOR20110397. Archived from the original(PDF) on 9 January 2007.
- ^ abHeras, Iñaki; Dick, Gavin P.M.; Casadesús, Martí (2002). 'ISO 9000 registration's impact on sales and profitability: A longitudinal analysis of performance before and after accreditation'(PDF). International Journal of Quality & Reliability Management. 19 (6): 774. doi:10.1108/02656710210429618.
- ^Naveh, Eitan; Marcus, Alfred (2007). 'Financial performance, ISO 9000 standard and safe driving practices effects on accident rate in the U.S. Motor carrier industry'. Accident Analysis & Prevention. 39 (4): 731. doi:10.1016/j.aap.2006.11.004. PMID17166474.
- ^Sharma, Divesh S. (2005). 'The association between ISO 9000 certification and financial performance'. The International Journal of Accounting. 40 (2): 151–172. doi:10.1016/j.intacc.2005.01.011.
- ^Chow-Chua, Clare; Goh, Mark; Wan, Tan Boon (2003). 'Does ISO 9000 certification improve business performance?'. International Journal of Quality & Reliability Management. 20 (8): 936. doi:10.1108/02656710310493643.
- ^Rajan, Murli; Tamimi, Nabil (2003). 'Payoff to ISO 9000 Registration'. The Journal of Investing. 12: 71–77. doi:10.3905/joi.2003.319536.
- ^Lo, Liang Kang; Chang, Dong Shang (2007). 'The difference in the perceived benefits between firms that maintain ISO certification and those that do not'. International Journal of Production Research. 45: 1881–1897. doi:10.1080/joi.00207540600733709 (inactive 12 July 2019).
- ^Buttle, Francis (1997). 'ISO 9000: Marketing motivations and benefits'. International Journal of Quality & Reliability Management. 14 (9): 936–47. doi:10.1108/02656719710186867.
- ^Santos, Leticia; Escanciano, Carmen (2002). 'Benefits of the ISO 9000:1994 system: Some considerations to reinforce competitive advantage'. International Journal of Quality & Reliability Management. 19 (3): 321–44. doi:10.1108/02656710210415703.
- ^Alcorn, Janice E. (2008). 'The Benefits of ISO 9000 Certification'. A Collection of Papers Presented at the 55th Conference on Glass Problems: Ceramic Engineering and Science Proceedings. Ceramic Engineering and Science Proceedings. 16 (2): 15–18. doi:10.1002/9780470314661.ch3. ISBN978-0-470-31466-1.
- ^ abcdThe ISO Survey of ISO 9001:2000 and ISO 14001 Certificates – 2003(PDF), International Organization for Standardization, p. 17, archived from the original(PDF) on 17 January 2012, retrieved 20 November 2015
- ^ abcdThe ISO Survey – 2008(PDF), International Organization for Standardization, p. 11, archived from the original(PDF) on 5 August 2011, retrieved 20 November 2015
- ^ abcThe ISO Survey of ISO 9001:2000 and ISO 14001 Certificates – 2003(PDF), International Organization for Standardization, pp. 1–2, archived from the original(PDF) on 31 October 2015, retrieved 20 November 2015
- ^ abThe ISO Survey of Management System Standard Certifications – 2011(PDF), International Organization for Standardization, p. 1, archived from the original(PDF) on 27 January 2013, retrieved 20 November 2015
- ^ abThe ISO Survey of Management System Standard Certifications – 2014 (data table), International Organization for Standardization, retrieved 16 September 2016
- ^ abThe ISO Survey of Management System Standard Certifications – 2014(PDF), International Organization for Standardization, p. 1, retrieved 20 November 2015
- ^Source: ISO Survey 2010
- ^'ISO quality management principles'(PDF). Iso.org. Retrieved 16 December 2016.
- ^'Using Quality Objectives to Drive Strategic Performance Improvement'. Qualitydigest.com. Retrieved 18 August 2017.
- ^'OBJECTIVE OF THE SAMPLE MANUAL'(DOC). Isopocketguides.com. Retrieved 18 August 2017.
- ^ISO/IEC 17021: 'Conformity assessment. Requirements for bodies providing audit and certification of management systems' (2011)
- ^ISO/IEC 17011: 'Conformity assessment. General requirements for accreditation bodies accrediting conformity assessment bodies' (2004).
- ^'25 Years of ISO 9000 A View from the Q'. ASQ. Retrieved 20 April 2016.
- ^Bacivarov, Ioan (1 October 2015). 'The Standard ISO 9001:2015 - A Milestone in the Evolution of Quality Management'(PDF). Asigurarea Calitatii - Quality Assurance. Retrieved 14 October 2015.
- ^'Infographic: ISO 9001:2015 vs. 2008 revision – What has changed?'. Maritime Cyprus. Retrieved 9 October 2018.
- ^'ISO 9001 Quality management'. ISO. Retrieved 18 December 2018.
- ^'ISO 9001:2015 - Just published!'. ISO. Retrieved 2 October 2015.
- ^'BSI obtains first global accreditation from ANAB to certify organizations to the new Quality Management standard ISO 9001:2015'. BSI. Retrieved 4 September 2015.
- ^ abcSroufe, Robert and Sime Curkovic, 'An examination of ISO 9000:2000 and supply chain quality assurance.' Journal of Operations Management, Volume 26, Issue 4, July 2008, Pages 503-520
- ^ abWade, Jim (May – June 2002). 'Is ISO 9000 really a standard?'(PDF). ISO Management Systems.
- ^ abcdBarnes, Frank (Spring 2000). 'Good Business Sense Is the Key to Confronting ISO 9000'. Review of Business. Archived from the original on 27 February 2009.
- ^'Debunking the myths'(PDF). Iso.org. International Organization for Standardization. Retrieved 7 July 2017.
- ^Dalgleish, Scott (5 May 2003). 'Probing the Limits - ISO 9000: More Hindrance Than Help'. Quality Magazine. Retrieved 10 June 2015.
- ^ abHenricks, Mark (December 2001). 'ISO a GO-Go'. Entrepreneur Magazine.
- ^Dalgleish, Scott (1 April 2005). 'Probing the Limits: ISO 9001 Proves Ineffective'. Quality Magazine. Retrieved 6 June 2015.
- ^'The ISO Survey – 2005'(PDF). Abridged version. ISO. 2005.
- ^Abrahamson, E. (1996). 'Management Fashion'. The Academy of Management Review. 21 (1): 254–285. doi:10.5465/amr.1996.9602161572. JSTOR258636.
Further reading[edit]
- Bamford, Robert; Deibler, William (2003). ISO 9001: 2000 for Software and Systems Providers: An Engineering Approach (1st ed.). CRC-Press. ISBN0-8493-2063-1, ISBN978-0-8493-2063-7
- Naveh, E.; Marcus, A. (2004). 'When Does the ISO 9000 Quality Assurance Standard Lead to Performance Improvement? Assimilation and Going Beyond'. IEEE Transactions on Engineering Management. 51 (3): 352. doi:10.1109/TEM.2004.830864.
- Naveh, E. (1999). ISO 9000 survey'99: An analytical tool to assess the costs, benefits and savings of ISO 9000 registration. QSU Publishing Company.
- Bacivarov, Ioan (Coordinating Editor) (2015). Special issue 'ISO9001:2015'. Asigurarea Calitatii - Quality Assurance 21 (83), ISSN1224-5410
External links[edit]
- ISO/TC 176, SC 2 - ISO committee responsible for developing ISO 9000 standards
Too often management sighs when they know they have another one of those “ISO meetings.” I would too if it consisted of listening to one person, the quality manager, report on his or her findings for an entire hour using “ISO” language no one else understands.
I mean the ISO standard tells you exactly what you need to discuss and report on during these management review meetings. What could go wrong, right?

Well, if the quality manager is the only one talking throughout the meetings and rigidly sticks to an agenda of items using “ISO” language no one else understands, can you blame management for the sighs when they are reminded of another management meeting?
Management Review Pdf
Think about it…how fun is a conversation when the other person never lets you get a word in? You have to listen to their stories and when you go to interject, they just talk louder and continue on.
On the other hand, there are those you have a conversation with where one hour with them feels like five minutes. Why? They talked, you listened and when you talked, they listened!
This is a good lesson to take into how we set up our management review meetings. Treat your management review meetings as a platform for members of your team to discuss what they see working well and not working so well within your quality management system. If you, as the quality manager, take a step back during these meetings to listen to what others are saying they can really reveal true issues within your system. I explained what works well DURING a management review meeting in a previous post (click here to read it).
What To Do When the Meeting is Over?
While what you do during the management meeting is important, the actions you take afterwards and your organization of discussion topics is even more important.
Iso 9001 Management Review Meeting
If you’ve listened to your management team and took copious notes, you didn’t have time during the meeting to organize what was discussed and fit them into the various input requirements from Clause 5.6.
Your job is not over when the meeting ends because now you need to organize your notes and what was discussed so you can create any follow-up actions, complete any corrective action forms, and ensure any problems discovered don’t get overlooked. When problems are not solved or followed up on, your product or service quality will start to slip.
In order to stay accountable to topics discussed at management review meetings it is important to create a chart or table to organize what are called action items. Here is an example:
(Note: This is not a complete table..just enough examples to ensure you understand) Driver for wd 1200jb.
Notice how this particular Action Item table is organized by department. Another way to organize it is by the management review outputs listed in clause 5.6 in the ISO 9001:2008 standard. Here is what that would like look:
(Note: This is not a complete table..just enough examples to ensure you understand)
As you can see in the two example tables above, each category, if discussed at the meeting, has an action plan for the next meeting. Each action plan is responsible to one person and a description of how they plan to do it is listed as well. This method of objective, person responsible, and action plan ensures issues discussed at your meetings are not forgotten about. There may not be an action item for each department every management review meeting. However, if a problem or concern is raised at a meeting, it is important management decides on an action plan to remedy it.
Also notice in both examples how previous action items are followed up. In the management section of the Management Review Notes Table 1 there was a problem at the last meeting concerning “filling out final inspection forms.” The result was 29/39 final inspection forms were completed in the previous month. Management decided to keep this same action item but increase percentage complete for the next meeting: “improve final inspection form completing to 85%.” This action item is listed second in the far right column. Depending on if this goal is reached or not at the next meeting will determine how long this action item needs to be followed up upon.
Iso 9001 Management Review Examples
Sometimes it may take your organization two or three meetings before a particular action item or problem is finally solved in a way you are happy with. This is ok! There is no ISO requirement that problems need to be solved in “x” amount of time. What is important to an auditor is seeing your organization is dedicated to talking about quality management issues and taking actions to fix them.
Here is a list of other actions you should be taking as a quality manager after management review meeting:
- Review notes and input necessary information into meeting minutes template of your choosing.
- Ensure action items identify due dates, personnel responsible, and any actions to be taken.
- Send completed management meeting minutes form to management. It is especially important for those management members with an action item for the next meeting to receive a copy.
- Set a date for the next management review meeting.
- Make a plan of action to follow up on actionable items before the next meeting.
Please let me know in the comments section below if there are any other steps you take during your management review meetings to ensure their success.